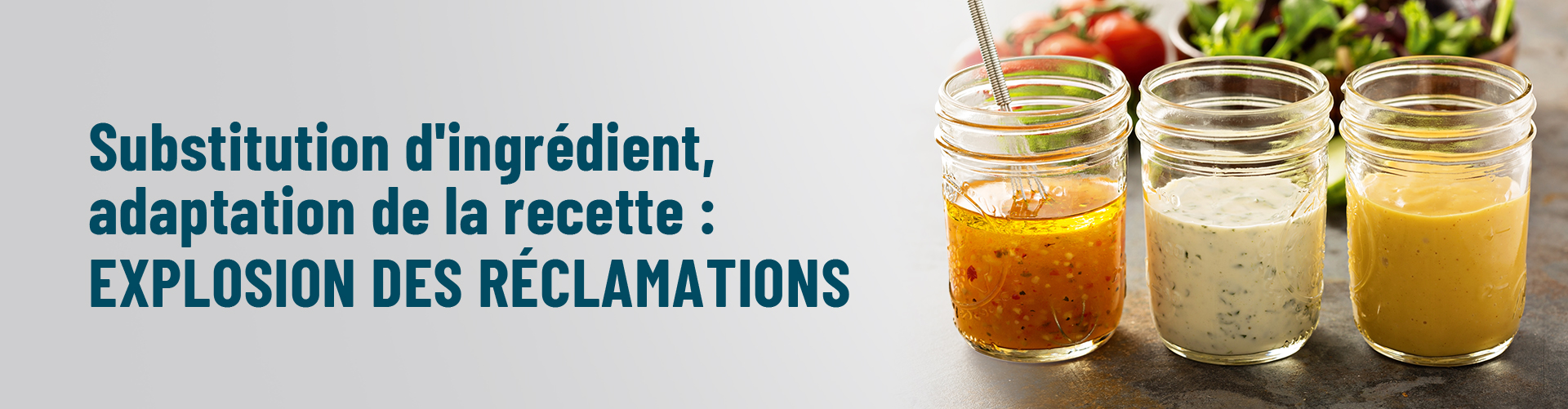
HOW TO IMPROVE QUALITY MONITORING THROUGH COMPLAINTS?
You are missing one product info...
In view of the next IFS audit in 15 days, Damien, a trainee in the Quality Department of Soprodal, reviews the 6 chapters and 278 points of the checklist of the standard. Samia, his manager, has asked him to be very critical, but he can't find anything to say. He could nitpick, but he couldn't find a flaw. All of a sudden, something clicked! He remembers the Director's greeting on his arrival at the factory: "Above all, think customer". He drops his standard, goes for a store check and buys a few products from Soprodal. One of them is a private label "BBQ Kit" with chilli, tartar, curry and cocktails, which he will taste this evening with his flatmates. The tasting is appreciated, except for the jar of tartar. Indeed, he finds it tastes funny. We are close to the expiry date but he knows that this answer is not acceptable, the product must keep its qualities until the end.
Consumer complaints: an indicator to assess the evolution of quality throughout the product life cycle
The next day, back at the factory, he checks other samples. Several had the same earthy taste, which was not exactly pleasant. It was the monitoring of the complaint rates that confirmed his idea that there was a problem with this product. In fact, not only is the complaint rate higher than for other sauces, but it has also gone through two successive levels in recent years, which shows that this dissatisfaction is changing.
Product modifications outside the process: a risk!
Logically, he then looks for the ageing validation study. Acidity, pH, stability tests, microbial validation, everything is available. But as far as the organoleptic aspects are concerned, apart from a few follow-ups after production: "RAS / Normal / Standard / A little salty", there is no real validation file. However, all the people we spoke to were certain that the ageing study had been carried out. But where is it? Centralisation of information on a single workstation, the departure of an executive, loss of backups, change of messaging system, so many reasons for the elements compiled at the time of product creation to disappear over time. And when Damien finally finds the paper validation file, he realises that the formula has changed several times since it was launched:
- Cost reduction project ⇒ fat was reduced.
- Optimisation of purchases ⇒ the supplier of capers has changed.
- Search for naturalness ⇒ the original aroma has been replaced.
These are all reasons for a different organoleptic evolution. Modifications that did not generate new conservation monitoring. The point was not even mentioned. "It's optimization, not development...". The evolution of the product was done outside the process.
If only the dates of these changes were known, we could compare the complaint rates before and after the changes. Two major flaws in the system.
That's it. The audit is coming...
The complete history of a product should be centralised and quickly available in case of an alert, including consumer complaints
But internally everyone has learned their lesson. With the multiplication of references and modifications, no one really controls the products anymore. We are moving away from the subject, from the consumer. Organisations are changing and the dispersion of documents and data leads to a loss of information with each change. Procedures have become so complex that they are not adapted to the normal evolution of the life of products. Alerts" through changes in the rate of complaints are not exploited.
We need to organise ourselves differently and rethink the management of product data.
How can you be sure that all the data relating to a product exists and is up to date?
How to manage successive "small" changes?
How can consumer complaints be used as effective warnings of abuses during the life of a product?
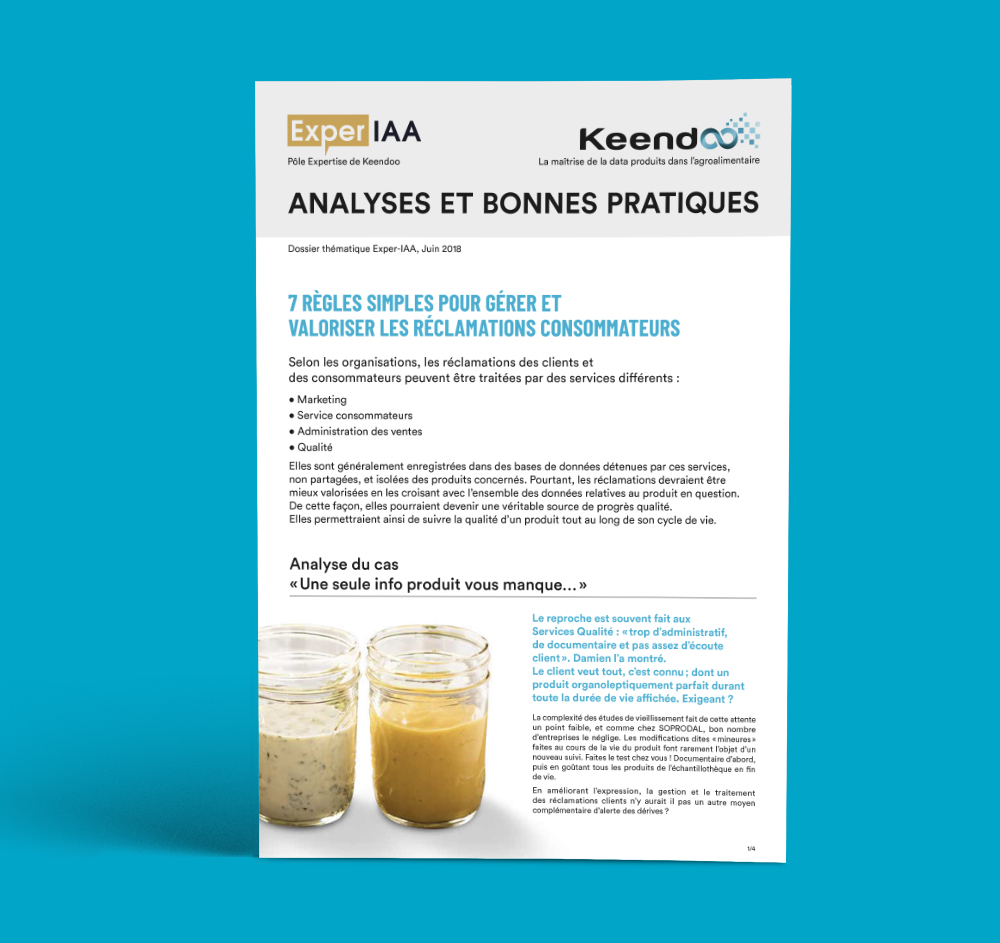
To find out more, download our thematic file